Foundry
Project Foundry | |
---|---|
Status | In progress |
Contact | User:Semafoor, User:Gori |
Last Update | 2016-01-14 |
Goal
To make a foundry capable of melting reasonably large amounts of metal, more specifically aluminium, brass and bronze. In my wildest dreams also cast iron, but that may not be realistic
Furnaces
Initial design
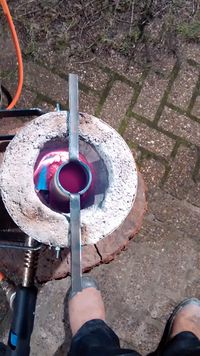
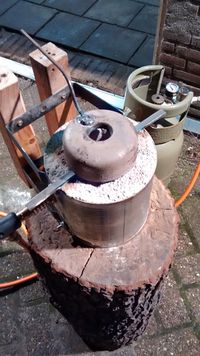
Gori made a small foundry out of a soup can, a propane blowtorch and some refractory. This works reasonably well and never fails to gather a crowd. It only melts approximately 0.2 l of aluminium, and this is clearly not enough to do any real work.
Second incarnation
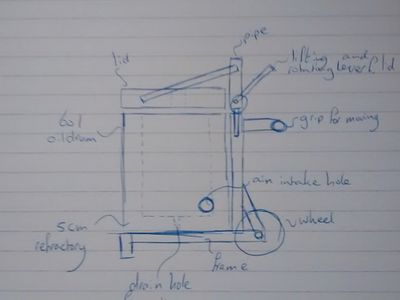
Semafoor is gathering materials to build a second, much larger furnace out of a 60 l oil drum. Should look something like this >.
Key points are:
- Movable on its own wheels because it will be heavy
- A lid to reduce the heat loss at the top (big problem in the soup can furnace
- Incorporated device to lift the lid up and to swing it to the side
- Lid will be mounted on a tube that will slide into a larger tube of the frame
- Lever + Cam to lift the lid a couple of cm, to be clear of the bottom part of the furnace
- Same lever will be used to swing the lid sideways
- about 5 cm of refractory all around. Probably a bit more on the lid for rigidity
- Electric blower to provide more air for combustion > more fuel > more heat
- Fuel: Not sure yet. Possiblities are:
- Propane: moderate initial investment. Relatively expensive to run. Easy to run. Cleanest fuel.
- Waste oil: Motor oil or vegetable oil. (nearly) free to run. easy to run, quite clean when running. Vegetable oil would be CO2-neutral as well. Most hackable fuel (dedicated fuel system and all)
Build status
Barrel
A 60l oil drum has been acquired. It now needs to be separated into a part for the lid and a part for the lower body. The lid needs some reinforcement to be lifted and to keep the refractory in. The lower body needs a drain hole (in case of crucible failure, to let the molten metal out) and an air intake hole for the burner flame.
The dimensions of the barrel are 590 mm high and 375 mm diameter. With a suspected 50mm refractory lining this should give an inner diameter of around 250 - 275 mm. Inner height would be around 450 mm (excluding a plint for the crucible to sit on. Maximum crucible dimensions should be around 200 - 250 mm outer diameter, and a height of 350 - 400 mm.
Frame
The frame needs to
- support the furnace body
- be strong enough to transport the entire furnace on its wheels
- support the lid lifting and lid rotating mechanism
The wheels for the foundry are probably the first thing to cast using this furnace, as an (easily replaceable) aluminium wheel would be sufficiently heat resistant.
Burner
Depends on whether propane or waste oil is used
Blower
Three blowers are available:
- Low power dual 115V Xerox blower
- medium power domestic heating blower
- reasoably high power forging blower aquired through Pietdv
Refractory
Good things to have in a refractory
High alumina content
Air pockets (for improved thermal insulation) by adding (Styro-)foam beads
Fireclay (no idea what this is called in Dutch
Kaolin clay
Chammotte clay
Grog / ground bits of firestone / chammotte stone
Bad things to have in a refractory
Portland cement: breaks down around 550 degrees Celsius
(silica) sand: At high temperatures the crystal structure expands, resulting in cracked refractory
bentonite: also known as kitty litter box filling. Not sufficiently heat resistant.
Materials that may be good or bad (unsure)
Perlite: good insulation, not super good at high temperatures
Molds
Probably sand casting, see Backyardmetalcasting.com or AlloyAvenue
Cope and drag
Some builders sheeting will be used for construction of the cope (top) and drag (bottom), most likely underlayment or OSB (course particle board). Plenty of 44x44 mm timber is available in the sparkshack to reinforce corners, be used as handles and so on.
Greensand
Greensand is used in the molding proces to form the actual casting cavity. Water bonded green sand is easiest at first and consists of the following:
- sharp play sand
- bentonite clay - As little as possible to make the sand stick together (around 10%)
- small (small!) amount of water, just enough to make it stick together
Crucibles
Wvholst as found some fancy Silicon carbide graphite crucubles on Aliexpress. These are definitely worth looking into when everything is in proper operation. Before that time, a steel crucible (welded from pipe, or just from some fire extinguisher bottle or something like that) should give us a dozen or so melts to get acquainted with the process
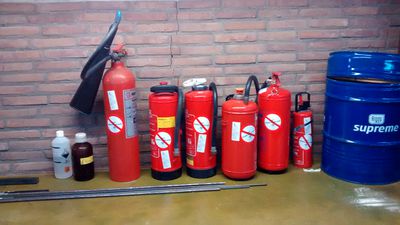
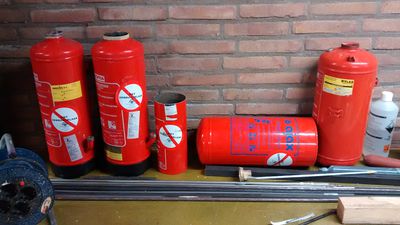
Literature and references
Foseco's Non-ferrous foundryman's Handbook
Prometheus' The Hobbyist's Guide to casting metal